Bombsheller: The website that makes us all into top fashion designers
Seattle company lets customers create their own clothes, then click 'buy' and wait for delivery
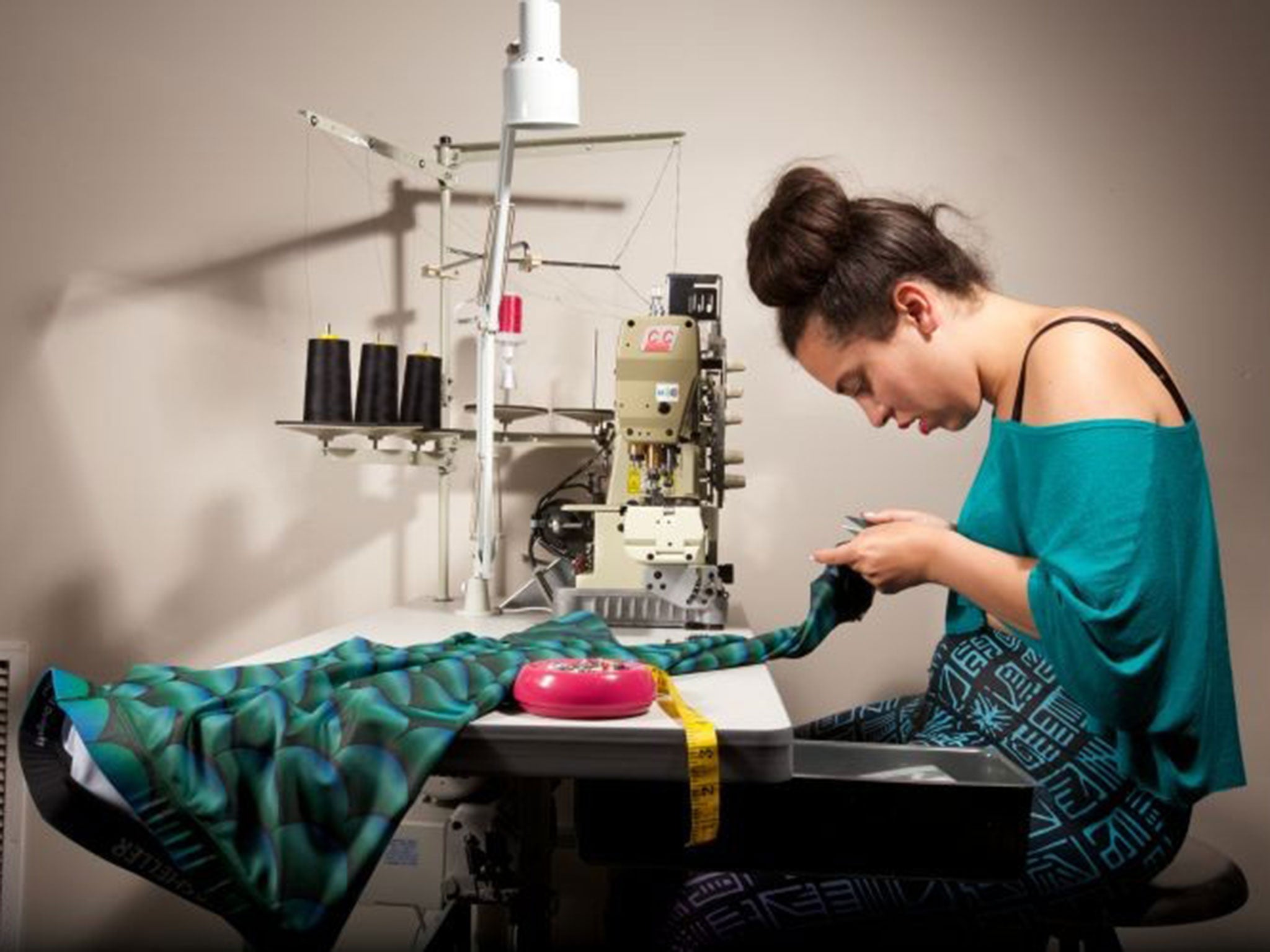
With its image of dapper tailors wielding tape measures in Savile Row fitting rooms and seamstresses labouring over yards of expensive silk, bespoke fashion has long been the natural domain of country squires and the more monied followers of fashion.
But if a former computer hacker who counts Bill Gates among his clients, and once invented a machine for quelling hurricanes, gets his way, buying clothing that is made-to-measure – and also carries the design or image of your choice – will soon be routine and affordable to those who shop in Gap rather than Gucci.
Pablos Holman, a computer programmer turned would-be fashion mogul, has opened the world's first fully programmable clothes factory designed to deliver customised garments by return of post.
His Seattle-based company, Bombsheller, opened for business last month selling customisable leggings, and has chosen Britain for its second computerised factory. He believes it will allow more consumers to create their own clothing but will also return manufacturing in the £1trn global apparel industry from the Far East and the Indian sub-continent to Europe and North America.
The desire to place an individual mark on things to wear is being picked up increasingly by established brands and retailers. Burberry, the British designer brand, will offer a range of monogrammed ponchos – at £895 a pop – from September, while Jimmy Choo has begun offering customisable options for five of its shoe styles: heel height, material, and a monogram on the sole.
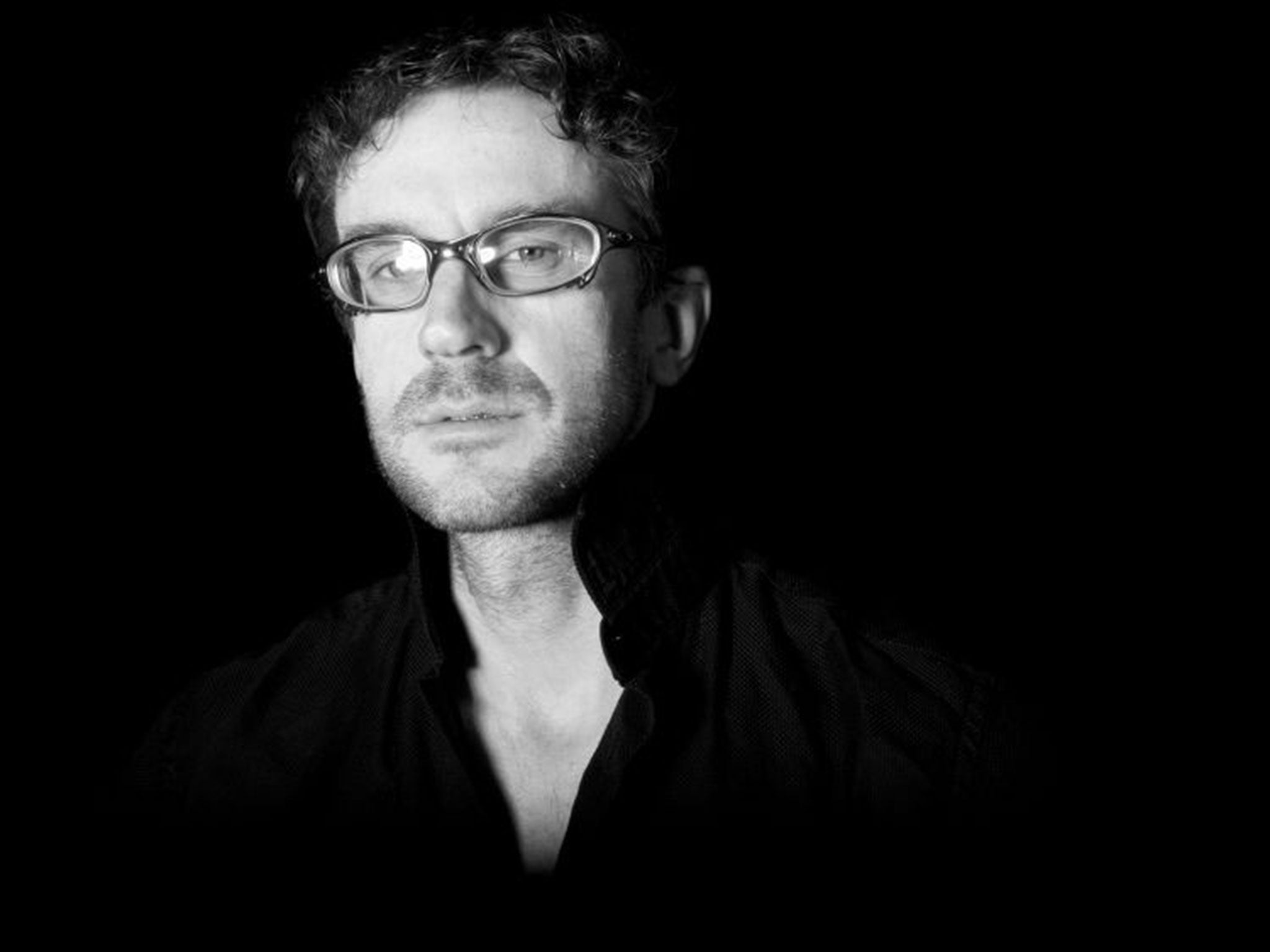
At the high street end of the market, Adidas will soon allow customers to print an Instagram image on to the heel of its trainers.
But while established manufacturers are tweaking their processes, Mr Holman argues that the flexibility of computing has the potential to disrupt the current model of clothes manufacturing which is reliant on bulk ordering and sweatshop-style labour.
The new company operates via the internet, allowing customers to submit their own eye-catching designs for leggings as well as modifying sizing and even the length of the garment. It is then delivered free worldwide for about £40.
He said: "The cycle for fashion is too long and constrains creativity – it takes months from concept to product. Also, manufacturing costs heavily skew towards large runs – you have to make thousands of the same thing and clothes are made for lowest-common-denominator humans – small, medium, large.
"Fashion has a lot to gain by welcoming computer technology. We can change the economies of scale so that it is just as profitable to make one of something as it is to make 1,000. We can reduce the environmental damage caused by shipping materials all over the planet."
"We have no inventory and we don't make anything until somebody clicks 'buy now'. Computers print the design, in your size, and it is sewn by seamstresses who are getting paid 100 times as much as a factory worker in Bangladesh," he added.
Analysts agree that the opportunity to produce something unique is increasingly attractive to discerning shoppers. Sarah Pearson, of marketing consultancy Protein, said: "Consumers are looking for brands that offer a unique service and selling point to help them stand out from their peers. Digital technology is democratising the personalisation process, which was until now a luxury only reserved for affluent consumers."
Such blue-sky thinking is run of the mill for Mr Holman, 42, who once invented ways to hack into computer systems but now helps run Intellectual Ventures Lab – a subsidiary of a controversial investment company which has become one of America's largest patent holders, thanks to a bewildering array of inventions.
With wage costs rising in countries long used as pools of cheap labour, in particular China, British companies are increasingly looking to repatriate production, a process known as "reshoring". Hornby has returned much of the production of its Humbrol paint for models to Britain from China while Laxtons, a Yorkshire textile company, has returned its production from overseas.
While large-scale manufacturing of complex machinery – from cars to computers – will continue, Mr Holman and others believe the future is in small-scale production.
Join our commenting forum
Join thought-provoking conversations, follow other Independent readers and see their replies
Comments