How a new recycling process could help stop Christmas trees going to waste
Our old trees emit an estimated 100,000 tonnes of greenhouse gases when they go to landfill – but pine needles can now instead be turned into useful industrial materials
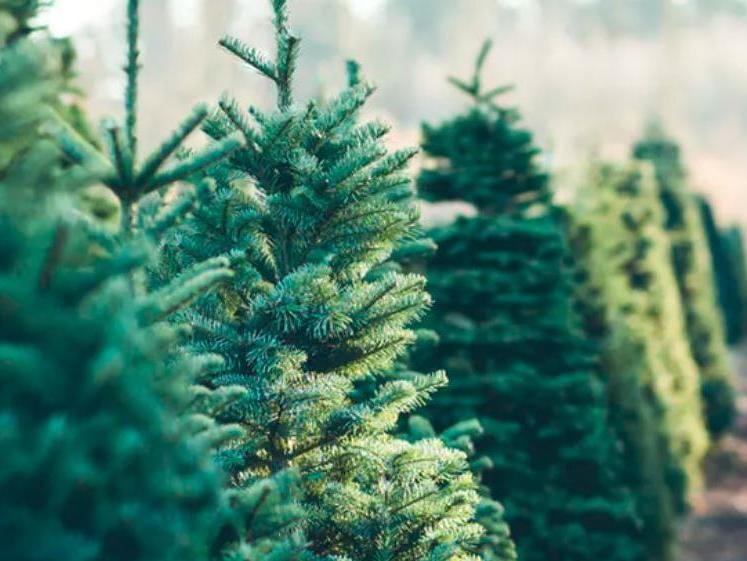
It wouldn’t be Christmas without a tree, but which is more sustainable – a real tree or a plastic one?
You might expect anything plastic to be the least environmentally friendly option. It’s true that manufacturing plastic trees consumes a lot of energy, and so does shipping them to the UK from where they’re commonly manufactured – China, for example. Although you can use a plastic tree for many years, most aren’t recyclable and still end up in landfill.
However, real trees aren’t necessarily the greener option. The UK uses as many as 8 million natural Christmas trees each year and sadly, about 7 million of these are discarded. The other million are mainly used as compost, though many people avoid this on the assumption that the low pH of pine needles (between 3.2 and 3.8) will make the soil acidic.
Christmas trees such as the Norway spruce and Nordmann fir have hundreds of thousands of pine needles which take a long time to decompose compared to other tree leaves. When they rot, they emit huge quantities of greenhouse gases.
According to the Carbon Trust, the carbon footprint of a 2m-tall real Christmas tree is equivalent to 16kg of CO2 if it ends up in landfill. That’s 100,000 tonnes of greenhouse gases from the 7 million trees that end up languishing in landfills every year.
A tree is for life, not just for Christmas
A better solution would be to reuse the pine needles and the trees. My research at the University of Sheffield has been investigating whether there are useful products that we can get from pine needles.
Like most plant biomass, 85 per cent of a pine needle is a structurally complex polymer known as lignocellulose, which is rich in carbohydrate and aromatic compounds. The structural rigidity of lignocellulose makes it unattractive and useless in most industrial processes because of the high energy intensity needed to break it down.
My research is focused on how the complex structure of this polymer can be broken down into simple industrial chemical feedstocks of high value and low molecular weight, such as sugars, organic acids and phenolics – chemicals that are important raw materials in industrial manufacturing.
By a process called liquefaction which uses moderate temperatures and environmentally friendly solvents such as glycerol or water, the pine needles are converted into a liquid with a solid byproduct called bio-char. The warm solvent helps to break down the complex chemical structure of pine needles into smaller chemical molecules, which make up the liquid.
This liquid product typically results in glucose, acetic acid and phenol. Glucose is used in the production of sweeteners for food, acetic acid in making paint as well as adhesives and even vinegar, and phenol for making medicines.
None of the products from this process are wasted – even the bio-char can be used as a catalyst for other chemical reactions.
The tree doesn’t need to be fresh either, as the process applied in this work can effectively handle both dry and wet biomass, eliminating the need for an expensive drying process. This is a key advantage of the liquefaction technique over traditional technologies such as combustion and gasification, whose efficiency depends on the moisture content of the biomass.
This method also works well with other forms of biomass waste and can be used for any species of pine. An industry built on this process could convert much of the available biomass waste from food crops and forestry management into vital products.
Aside from converting biomass waste into precious materials, this process adds value to otherwise less useful solvents such as crude glycerol – an unwanted byproduct from the biodiesel manufacturing industry. Using glycerol increases how much of the biomass waste can be converted to liquid product compared to the commonly used water process, known as hydrothermal liquefaction. More than 90 per cent of pine needle mass is converted in the presence of glycerol compared to only 60 per cent with water.
The benefits of this research are huge. It can help reduce carbon emissions by decreasing dependence on imported artificial Christmas trees and limiting the amount of biomass sent to landfill.
If commercially feasible, this could make industrial processes more sustainable by creating new products from something previously considered waste. Long after the festive period is over we could continue using this method to recycle forest and agricultural waste on a much larger scale, bringing greater benefits throughout the year.
Cynthia Kartey is a PhD researcher in chemical engineering at the University of Sheffield. This article first appeared on The Conversation (theconversation.com)
Join our commenting forum
Join thought-provoking conversations, follow other Independent readers and see their replies
Comments