The workers left behind by Donald Trump’s Carrier jobs rescue
As President-elect, billionaire businessman announced deal with parent company United Technologies to prevent plant relocation to Mexico - but not everyone's role was saved
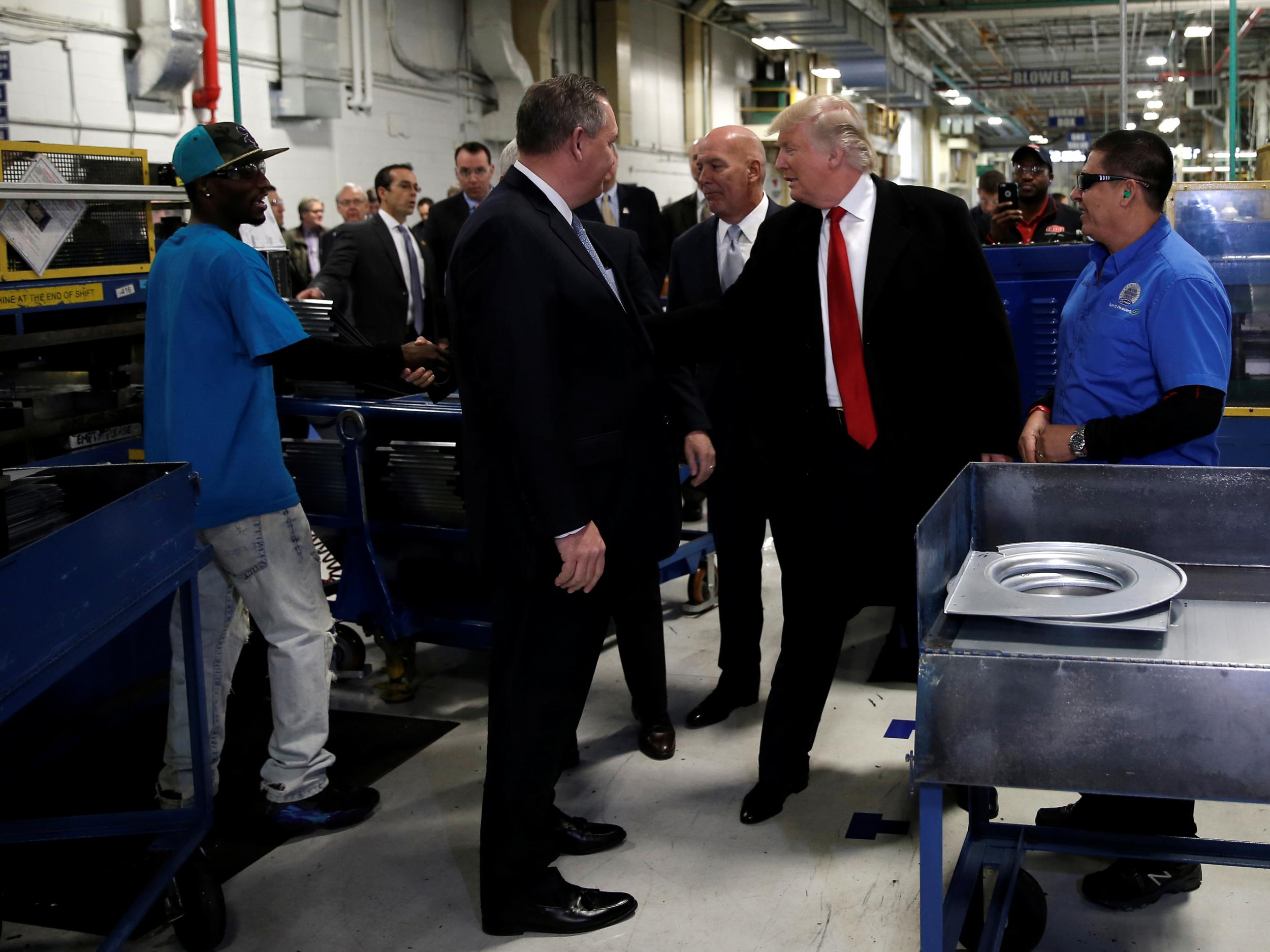
After assembling circuit boards for Carrier furnaces at a factory here for 21 years, Jim Sholle, 56, walked out of the plant for the final time last month. But he still finds himself waking up every morning at 4:30, ready to work the 6am-to-2pm shift.
“I’m a routine guy, and I’m not boohooing,” he said. “But I feel used up.”
Pat Saylors, 57, is still employed, but her days here are numbered, as they are for more than 700 other blue-collar workers. Production is set to end by late December at the plant, this town’s largest private employer, and each month several dozen of them are being let go.
“I loved my job,” said Saylors, who earns $17.31 an hour as a materials specialist, readying parts for the workers on the assembly line. She joined the company 40 years ago, when the plant was in tiny Converse, and then followed her job to Huntington when the factory here opened in 1990.
Saylors is typical of the factory’s workforce, which is mostly female, with an average age around 50. She joined a few months after graduating from high school, as did her daughter Amanda, who is 33.
“It’s all I’ve ever known,” she said.
During Trump’s campaign, the fate of more than 2,000 Carrier jobs that the company wanted to move to Mexico from Indiana, including those in Huntington, were Exhibit A in his attacks on the free-trade policies of his predecessors, both Democratic and Republican.
So when President-elect Trump announced on Thanksgiving that he was near a deal with Carrier’s corporate parent, United Technologies, to save them, Sholle and Saylors thought they were among the lucky ones.
It was not to be. Thanks to public pressure from Trump and a generous package of tax breaks negotiated by Governor Mike Pence, now the vice president, Carrier did agree to keep making some of its furnaces in Indianapolis, preserving roughly 800 of 1,400 jobs there.
But the plant in Huntington operated by United Technologies Electronic Controls, or UTEC, was not part of that deal — nor would it be helped by the “buy American” mandate for federal infrastructure projects Trump promised in Wisconsin last week. And by early next year, the components used for furnaces still assembled in Indianapolis will come instead from Monterrey, Mexico, where it takes a day to earn what workers here make in about an hour.
The economy in Huntington, a town of 17,000 in rural northeast Indiana, is quite different from what workers in Indianapolis face, however, as is the culture. Despite some notable closings, many factories remain, with 21 percent of local workers employed in manufacturing, a higher proportion than in more than 90 percent of the other counties in the country.
And as Sholle’s reluctance to complain suggests, the anger about the economy and about Washington that was so evident in Indianapolis and other parts of the Midwest that Trump carried is more muted here. Not that it’s absent — more than 70 percent of Huntington County voters supported Trump — but the pain is further below the surface.
For the most part, the workers do not fault Trump for failing to preserve their jobs, even as he took credit for keeping the Indianapolis plant open.
“I support him 100 percent,” said Tami Barnett, a 27-year veteran who left at the end of March. “I was very pleased he saved the jobs in Indianapolis. Do I wish he could have saved mine? Absolutely. But he did his best.”
Susan Cropper, 55, who works in the plant with her sister, Sandy VanDiver, 58, said she did not regret voting for Trump in November, either.
“I’m glad he stepped in, but it’s a letdown,” she said, adding that most of her fury was reserved for Carrier and its executives.
Asked about the failure to keep the Huntington plant open, a White House spokesman said last week that Trump was “incredibly proud to work with United Technologies to save nearly 1,000 jobs in Indiana and will continue to work with major companies to ensure he is doing all he can to increase American manufacturing, job creation and economic growth.”
Huntington’s mayor, Brooks Fetters, admits when pressed to being frustrated that he never heard back from Pence’s office after he called late last year to find out why Huntington was not helped.
“Right or wrong, that’s where we are,” said Fetters, a moderate Republican. “We’re not in panic mode.”
And in any case, he said, “German stoicism runs deep in northern Indiana, and you take your lumps.”
Huntington has managed to adapt by luring new metalworking and automotive suppliers in recent years, according to Mark Wickersham, director of economic development for Huntington County.
“We are not a dying town,” he said, citing the $1.4 million expansion last fall of a learning center opposite the high school, where teenagers as well as adults can earn certificates in fields like advanced manufacturing and health care.
Although retraining offers only modest hope for workers in their mid- to late 50s who possess only a high school diploma, Fetters insists the UTEC workers do not have to face a dismal economic future if they can learn new skills.
“At 4 percent unemployment, if you’re not working, there’s a reason and it’s not a good one,” Fetters said. “As mayor, I don’t have jobs for people who can just use a rake and a shovel. I do have jobs for equipment operators.”
The mayor is right — up to a point. It is true that local auto parts suppliers, machine tool makers and other industrial companies are hiring. But only a few positions are available at any time.
Not far from the soon-to-be-shuttered UTEC plant, with its parking lot full of late-model SUVs and pickups, Ecolab is hiring. The hourly wage is equal to what UTEC paid, but only four jobs are open at the plant, which makes soaps and sanitizers, with two of them offered to United Technologies employees.
Beyond that, Ecolab’s 100-strong workforce is not expected to rise significantly, according to Tracey Hartman, the company’s human resources manager in Huntington.
Like other longtime workers, Sholle received a severance package, including a $17,700 payment in his case. But he worries that he is not healthy enough to start over at another factory, and after he paid out $10,000 to cover taxes and medical expenses, the severance does not buy him that much time. His health insurance runs only through September.
More than a means to a paycheck, working in the UTEC factory was a way of life, with female workers especially developing the kind of deep bonds more common in small towns than big cities.
“We weren’t blood family, but we were family,” said Barnett, who worked in aftermarket sales and service. When she had a heart attack and needed quadruple bypass surgery in 2007, colleagues held bake sales and donated close to $2,500 to help her offset the loss of income during her 14-week recovery.
“That’s a lot of money to me, and I was overwhelmed by the caring and compassion,” Barnett said.
The decision last year to close the plant came as a shock, she added. “We made the company billions in profits. It’s a slap in the face.”
Workers like Barnett and Saylors might have been surprised, but outsourcing factory jobs was hardly a secret on Wall Street.
To improve earnings amid slow growth in recent years, a key strategy of United Technologies executives has been to shrink the company’s manufacturing footprint and move production to countries where labor is cheap.
At a meeting with analysts last month to discuss the outlook for 2017, the head of the division that includes Carrier, Robert J. McDonough, boasted that profit margins had doubled over the past five years.
“Part of it has been moving factories to lower-cost locations, there is no question about that,” he said. “I think everybody knows that’s been part of the formula for us.”
Why was Trump more successful in Indianapolis than in Huntington? “We were the redheaded, bucktoothed stepchild,” Sholle said bitterly. “We never even got mentioned in the coverage.”
There is some truth to the latter part of Sholle’s assessment. More than two hours north of Indianapolis and some distance from the nearest Interstate, Huntington, like other rural corners of the country, rarely gets much attention from outsiders.
At the same time, true to the spirit of its understated residents, Huntington’s political and union leaders shied away from the spotlight that their counterparts in Indianapolis sought out. Some feared that criticising United Technologies publicly would undercut negotiations to save jobs.
About 100 jobs in sales, marketing and engineering will remain in Huntington after manufacturing ceases, and the company has been adding to its white-collar staff here. Unfortunately, most of the workers on the assembly lines would never be considered for these jobs because they lack college degrees and other credentials, like engineering experience.
While it is too late for the likes of Jim Sholle and Pat Saylors, even United Technologies’ chief executive, Greg Hayes, suggested recently that the years of cost-cutting at Carrier, the furnace and air-conditioner maker, had gone too far, putting short-term profits ahead of long-term growth.
The need to stay competitive was the reason the company gave for moving the jobs from Indiana to Mexico, but Carrier’s market share actually eroded slightly last year. So Carrier is making a course correction.
“We need to make investments, as I said before, in the sales force,” Hayes told analysts on Wall Street in December. “We need to get more feet on the street.”
“Bob is focused on it,” Hayes added, referring to McDonough’s new marching orders to invest, in what sounded like a mix of goal and threat. “Bob’s senior leadership team is focused on it, and we’ve got to get everybody in the organization focused on it equally, so more work to do there.”
The New York Times
Join our commenting forum
Join thought-provoking conversations, follow other Independent readers and see their replies
Comments