Blood, sweat and tears: the truth about how your sportswear is made
Factories used by biggest brands abuse staff, employ children and pay pitiful wages – while stars earn a fortune
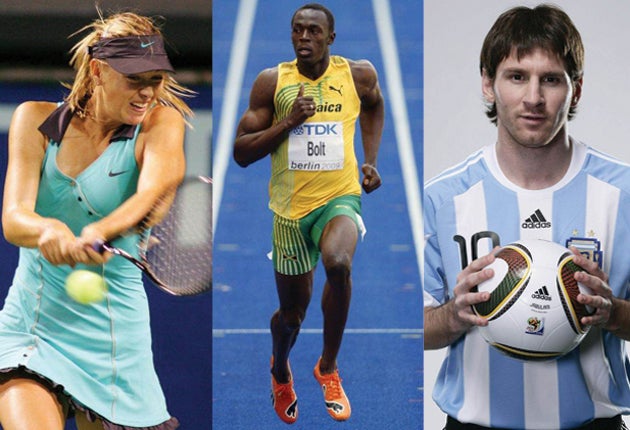
Your support helps us to tell the story
From reproductive rights to climate change to Big Tech, The Independent is on the ground when the story is developing. Whether it's investigating the financials of Elon Musk's pro-Trump PAC or producing our latest documentary, 'The A Word', which shines a light on the American women fighting for reproductive rights, we know how important it is to parse out the facts from the messaging.
At such a critical moment in US history, we need reporters on the ground. Your donation allows us to keep sending journalists to speak to both sides of the story.
The Independent is trusted by Americans across the entire political spectrum. And unlike many other quality news outlets, we choose not to lock Americans out of our reporting and analysis with paywalls. We believe quality journalism should be available to everyone, paid for by those who can afford it.
Your support makes all the difference.Many football tops, running vests and trainers on sale in the UK are made by sweatshop workers toiling long hours in hazardous conditions without trade union-rights, according to documents published by sportswear companies.
Two days before the Commonwealth Games begin, an analysis by The Independent of labour inspections by Nike, Puma and Adidas, the world's top brands, identified 281 rogue factories, whose failings ranged from the unsatisfactory to the abysmal.
Low pay and long hours are common in workshops but some also use bonded or prison labour, ban collective bargaining, threaten and harass workers and force women to undergo pregnancy testing. "Less productive" workers face the sack.
A decade after some shoppers boycotted Nike over the issue, the leading players in the £134bn-a-year global sportswear industry seek to protect their reputations against allegations they profit from sweated labour by inspecting factories and blacklisting the worst. However their own reports show they have had only partial success in cleaning up the industry, and that they continue to outsource production to countries where trade unions are banned or restricted.
Instead of the "living wage" sought by campaigners, they pay the legal minimum wage, which can be half the amount deemed necessary by unions and academics to meet the cost of food, shelter, healthcare and education for a small family. When challenged by The Independent, none of the firms denied that some of their supplier factories were "sweatshops".
Nike's corporate responsibility report for 2007/09 paints the most vivid picture of conditions for the million of mostly Asian workers stitching and glueing sports shoes and apparel. It shows occasional or routine abuse by 35 per cent of Nike's suppliers – affecting up to 280,000 workers.
Of 479 factories checked last year, on average 168 failed to meet Nike's standards, meaning they had "serious system failures" or a "general disregard" for codes of conduct. One in five failed to provide contracts, honour collective bargaining, occasionally used children or worked staff seven days a week without a break.
One in 20 flouted wage laws, used bonded, indentured, prison or child labour, abused staff, or carried out mandatory pregnancy tests.
Nike said that some factories with poor grades may have had only one problem. On pay – to which most reports pay scant attention – Nike told The Independent: "We believe that local wage-setting is best done by negotiations between workers, labour representatives, the employer and the government."
Of 362 factories that supply Puma, one in five – 75 – failed audits two years ago. About half of those flouted rules on hours and pay, and most endangered workers' health. Three-quarters failed to follow rules on the handling of chemicals. Puma says it is committed to trade union-rights, but it outsources to China and Vietnam, which restrict those rights. In its Team Talk report, Puma admitted: "Considering these limitations, the social standard on freedom of association and collective bargaining is admittedly difficult to enforce at many of our supplier factories."
Adidas, which was praised by the campaign group Playfair in 2008 for introducing complaints processes and for ending short-term contracts, gives little information about life inside its factories. Last year it ranked 60 per cent of 1,200 suppliers in the bottom three "compliance" ratings, but since it declines to explain the criteria, it is unclear how many failed audits. Last year the German firm warned 38 suppliers that they were so bad they could lose contracts.
Conditions may be worse than publicly stated because factories falsify wage and time records to pass audits. Puma acknowledged "many factories" covered up excessive working hours with two sets of time records – one genuine and one for inspections. The firm said: "It is common knowledge in our industry that software programs have been developed specifically for this purpose, with workers being coached on how to answer questions."
Campaigners say that despite their willingness to document abuses, sportswear firms could do more to tackle long hours and low pay. In a report for the 2008 Olympics, Playfair noted that substantial violations of workers' rights were "still the norm" and there was a "tendency to consolidate production" in states that restricted trade unions. Anna McMullen, of Labour Behind the Label, said: "They haven't acknowledged there is something called a living wage, never mind working towards it."
All three brands admitted that conditions could – and should – improve. Nike said: "Although we work quickly to address issues identified in audits, we know that challenges remain in some contract factories, including reducing excessive overtime and protecting the right to freedom of association."
Puma said the industry had made progress by effectively combating child labour and improving health and safety, adding: "In other areas, such as freedom of association and wage levels beyond the legal minimum requirements we still see challenges ahead."
Adidas said that as a result of its work it had been named a world leader by Dow Jones Sustainability Index.
Subscribe to Independent Premium to bookmark this article
Want to bookmark your favourite articles and stories to read or reference later? Start your Independent Premium subscription today.
Join our commenting forum
Join thought-provoking conversations, follow other Independent readers and see their replies
Comments