When selling off Tata Steel, perhaps we should think creatively and follow the lead of Detroit
By splitting the company into a "good GM" and "bad GM" in 2009, Detroit's General Motors managed to save itself
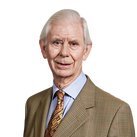
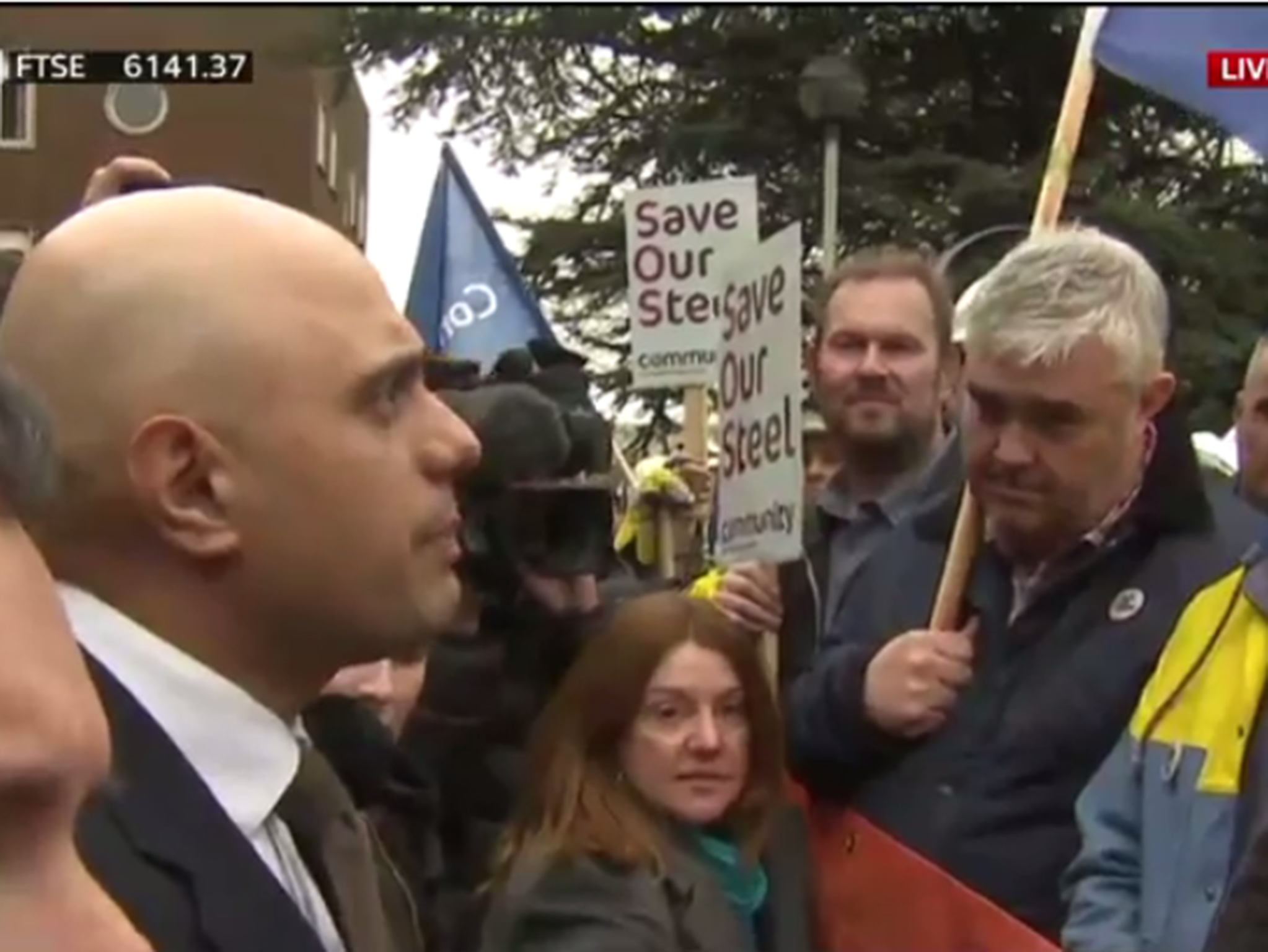
The process of selling off Tata Group’s steelmaking facilities in Port Talbot begins on Monday. At risk are 4,000 jobs at the plant itself. In addition there are some 25,000 workers in the supply chain. If a new owner cannot be found, closure would be a painful wound in Britain’s manufacturing capacity.
Is steel-making in Britain, which would almost disappear if Port Talbot shut up shop, strategic in any sense? People generally answer no. While steel is what is called a foundational product, being essential for many manufacturing and construction activities, it can be purchased freely on world markets.
Even British manufacturers of military equipment are content to look abroad for their supplies. Steel for Trident nuclear submarines, for instance, comes from France.
People therefore presume that the government’s role should be limited to facilitating a deal and to handling the social consequences of a massive reduction in employment if no buyer can be found.
For me, however, this conventional analysis doesn’t ring true. It is essentially defeatist.
Steelmaking is an important world industry in which Britain could again play a significant role. In 2001 we were the second largest producer in Europe after Germany; but since then Italy, France and Spain have overtaken us. Was that part of some inexorable process that we cannot reverse? I don’t believe so.
There are three different ways of moving forward worth examining. The first is the restructuring plan drawn up by the management at Port Talbot. By its nature it is likely to be well informed and to demonstrate the art of the possible.
The target is to move from heavy losses into profit. It envisages cost savings of some £350 million per annum. These would partly come from the 750 job cuts announced in January.
The plan would take two years to implement and would also require new investment. An idea of what this might mean can be drawn from Tata’s comment that some £2bn would be required to transform the plant into a producer of high-quality steel for advanced industries. In any case, Tata was not impressed and called the plan unaffordable and risky.
Sanjeev Gupta, the founder of the commodities group Liberty House, which already has some steel manufacturing interests in Britain, has a different vision for Port Talbot.
He starts from the fact that the country exports the highest level of scrap per capita in the world. “We export 10m tonnes of scrap and we consume 10m tonnes of processed steel. That does not make sense.”
Importing coal and iron ore to produce liquid steel is uneconomic, he says, when scrap can be recycled. And that is what he would want to do at Port Talbot.
Gupta told the BBC that any party looking at buying the Tata operations must accept that the “biggest problem is the blast furnace”. He added: “They are importing all the raw material to smelt steel. We feel we have an alternative suggestion which is to still make hot metal but to make it from local raw material rather than imported raw material.”
His plans for South Wales involved a “change of technology rather than ending liquid steelmaking”. This would, though, require massive investment.
There is one more place to look in seeking a solution to the Port Talbot crisis – and that is Detroit in 2009. For the giant General Motors (GM) was rescued from collapse by reorganising itself financially through the bankruptcy courts with the willing assistance of the US Government.
According to a contemporary report in a trade journal, GM was split into two entities: a “good GM,” which included the core Chevrolet, Cadillac, GMC, and Buick brands and the facilities to support those divisions; and a “bad GM,” comprising redundant/unprofitable plants.
The goal of the bankruptcy process was for the existing, overburdened automaker to turn over its best assets to a less debt-riddled “New GM.” The New GM was expected to emerge from court protection in 60–90 days as a leaner, more agile company with fewer brands, dealers, and long-term obligations. The leftover assets were to be sold off or shut down entirely.
The US Treasury provided $30bn financing and, along with the major trades union, ended up with a significant shareholding in the “good GM”.
Here, then, are three case studies relevant to the future of Port Talbot. Someone must mould them together into a workable plan.
That person could be a senior manager at Port Talbot, or Mr. Gupta, or the Secretary of State for Business, Sajid Javid. Who will take up the challenge?
Join our commenting forum
Join thought-provoking conversations, follow other Independent readers and see their replies
Comments