Japan Airlines crash: How the Airbus’ new fireproofing helped all 379 passengers survive
The massive Japan Airlines plane collision is the ‘first real test for a modern aircraft’ under distress and Airbus’s new lightweight carbon-fibre fuselege may have protected passengers from fire long enough for everyone to evacuate, experts tell Arpan Rai
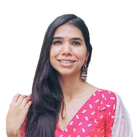
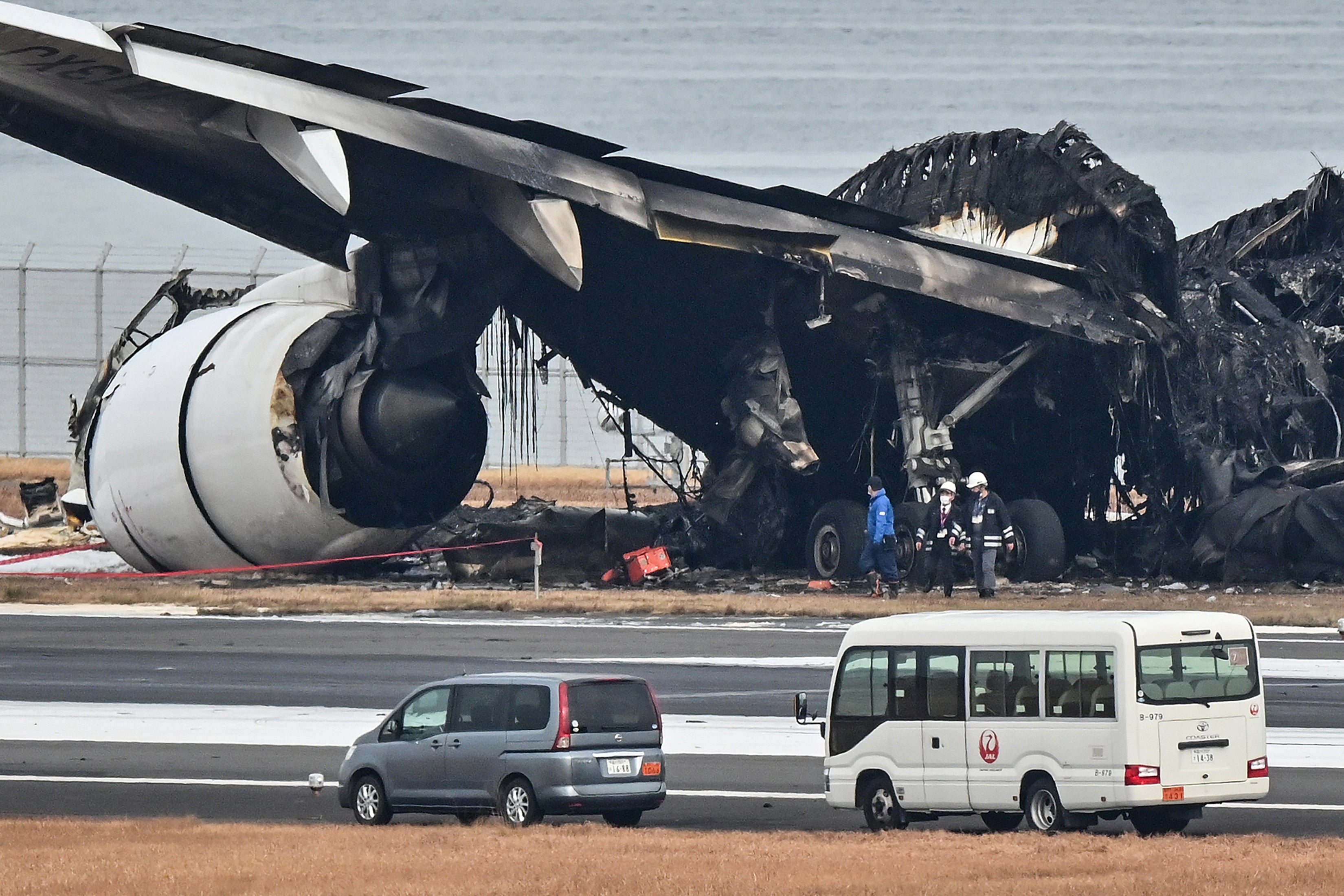
A lightweight carbon-composite fibre was dubbed a “game changer” for the Airbus A350 when it first entered the sector in the 2010s. Airbus called the carbon-fibre skin “more burn-through resistant than a metallic equivalent”.
But dramatic images of a Japan Airlines Airbus burning from nose to tail immediately after it collided with a coast guard jet on a Japanese runway has aviation experts both stunned and worried about the safety challenges of new composite materials.
This is the first time the most modern passenger jet known to humankind was tested in an accident, demonstrating the endurance of its body made of carbon fibre reinforced polymers (CFRPs) and potentially providing vital technological insights into the aviation industry’s favourite jet.
Six experts from the Japan Transport Safety Board reached the spot at Haneda airport in Tokyo to examine what remained of the aircraft on Wednesday as photos showed the severely damaged A350’s wings as the only identifiable pieces remaining of the plane’s charred and broken fuselage.
It’s a stark image, but Airbus suggests the endurance of the fuselage may actually be to thank for giving the Japan Airlines cabin crew precious time to evacuate all passengers.
Jon Ostrower, the editor-in-chief of The Air Current, an aviation analysis and reporting service, calls the massive collision the “first real test for [this] modern aircraft”. He says the incident is the first in commercial aviation history where an aircraft body made out of carbon fibre has been subjected to a major real-world fire.
The accident will provide “a massive trove of data” on how the material can withstand flames, he says.
The premier commercial passenger aircraft is assembled at Airbus’s final assembly line in Toulouse and its sections are manufactured at different sites around Europe, officials from the top-tier aerospace corporation said.
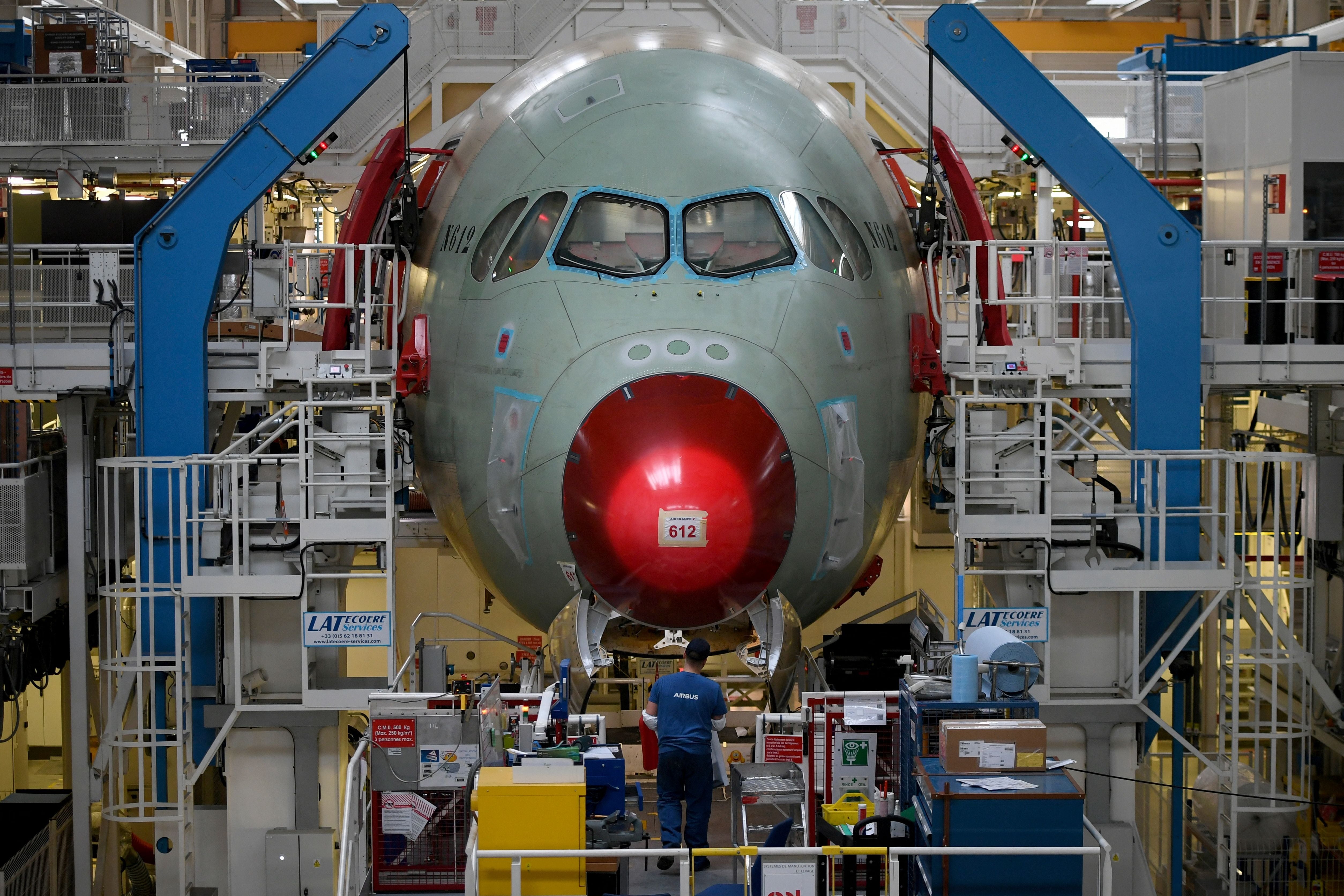
Over 70 per cent of the total airframe, which was left exposed on the Haneda tarmac on Monday, is made from advanced materials including composite materials, titanium and modern aluminium alloy, an Airbus spokesperson tells The Independent.
Officials at Airbus say they are not comparing the endurance and performance of different aircraft designs at the moment when an investigation is underway. But extensive tests have shown that composite structures offer a similar level of fire resistance and protection as aluminium, they said.
“The materials are significantly lighter, but just as robust as previously used metals. The aircraft has brought a step-change to the long-laul market, with a reduction in fuel consumption and carbon emissions of around 25 per cent compared to similar sized previous generation types,” the spokesperson says.
Tests by Airbus show the fuselage can also endure lightning strikes, bird hits, in-flight hail, uncontained engine failure, corrosion, fatigue of plane and of course fire.
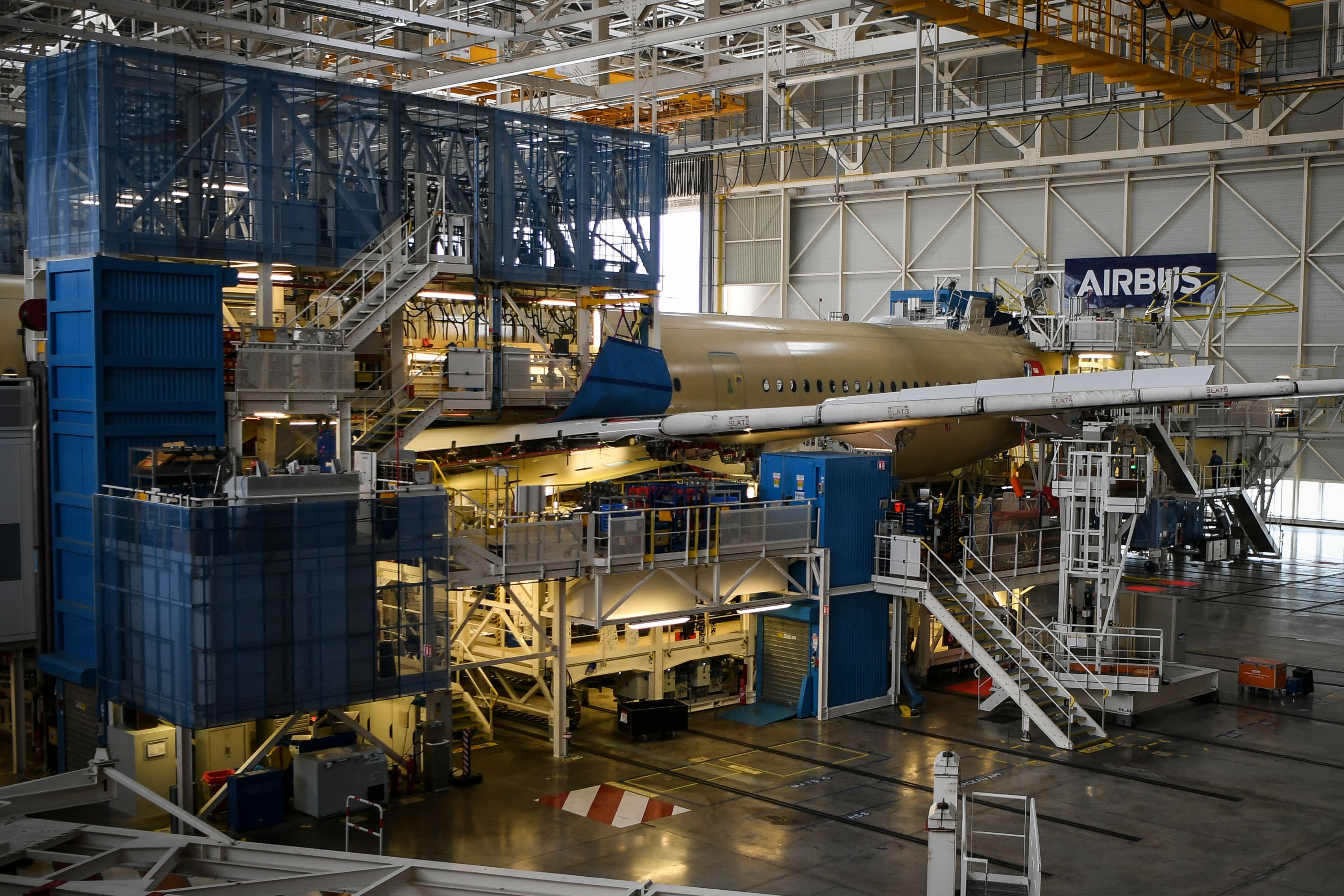
Aviation experts like Ostrower also point to how the aircraft’s carbon fibre structure was reacting to fire. “This is really something. Look at how the A350’s structure is reacting to fire. We haven’t seen anything like this with carbon fibre since the B-2 crash in Guam in 2008 – and the first time in modern commercial aviation,” he says on social media platform Twitter/X.
In a separate post, he added that “it’s hard to overstate how important of a moment this is in modern aircraft design”.
“Almost 400 people aboard that A350 and all got out safely after sustaining heavy damage. A lot of analyses and small scale tests on carbon fibre just got a massive trove of new data,” he said.
Alex Macheras, an independent aviation expert and consultant, said the fact the accident saw the complete loss of an Airbus A350 yet not a single death among those on board was “extraordinary”.
“Crucially, in the immediate aftermath of the collision, the fire seemed to be contained in the left wing area due to firewalls made of materials which become combustible at much higher temperatures to prevent flames spreading, long enough for the almost 400 people on board to safely evacuate the aircraft,” he says.
The aircraft, produced amid bitter competition from rival Boeing and its 787, entered commercial service in 2015. Airbus, which has sent specialists to help Japanese and French officials investigating the accident, said the plane in question was delivered to Japan Airlines in late 2021.
Join our commenting forum
Join thought-provoking conversations, follow other Independent readers and see their replies
Comments